Production Management and Process Control
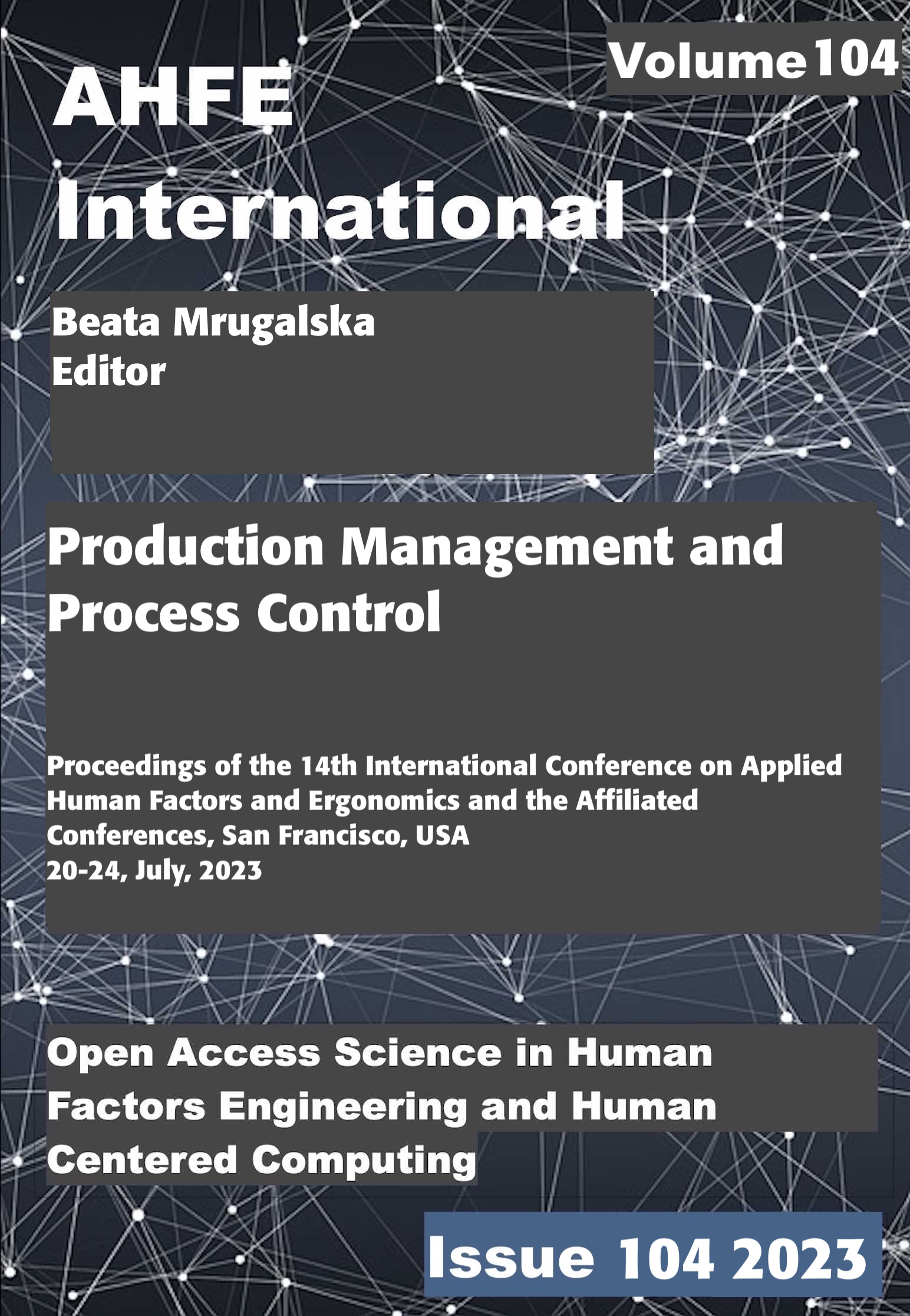
Editors: Beata Mrugalska
Topics: Production Management and Process Control
Publication Date: 2023
ISBN: 978-1-958651-80-3
DOI: 10.54941/ahfe1003045
Articles
Plant Engineer Performance Improvement for Effective Risk Reduction
To reduce the risk in the complex systems, it must be firmly suppressed in the original design process, so the safety concept is thoroughly incorporated into the system based on risk management at the design stage before operation. Next step, implement risk reduction measures are considered based on risk management at the construction or operation stages. As a response to the problem that remains even after taking measures in advance, that is, a risk that occurs at the stage of using equipment or processes, an failure or error is detected and the countermeasure is taken. Therefore, we will first understand the vulnerabilities at the time of implementation and the weaknesses in human relationships between organizations and teams. As counter-measures, it is the most important to give feedback to the hardware, next to software, and when it is not possible, it is important to take countermeasures by the organization or team, not to blame the individual fault. In summary, it is necessary to enhance human performance for dealing with problems that are anticipated in advance, and then to enhance error detection that remains even after setup.There are six measures to reduce risks. One is leveraging human performance tools such as Tool Box Meeting during runtime, and another is cause analysis as 5 why when the problem occurred. While effective risk reduction must be realized in the planning phase, in which there are four type of risk management activities. First, risk assessment by practical engineers at the field work planning, especially for the job situation at the first time, after a long time, or when job change. Second, on the contrary, long-term issues cleared by the feedbacks from various risk assessments in the plant and understood by executives. Third, risk analysis, which evaluates random failures or human errors, on the safety system (stand-by system). Fourth one is maintenance activities on the usual system based on failure physics. Total six approaches are completely different each other, and then sections to respond for them, not only safety, maintenance, quality assurance, but also executives, etc., are also different, that is risk management can be achieved by all members efforts in the plant.Risk reduction measures evaluation is the key for risk management in the plant. There are four methods to reduce risk. One is hazard reduction itself, such as change to small plant size or attach intrinsic safety features etc. Second is occurrence frequency reduction by preventive measures, installing barriers such as safety logic or safety systems, etc. Third is consequence reduction by installing mitigation systems. Fourth is consequence reduction by mitigating operation such as emergency planning, evacuation, etc. We must select the most effective way by discussions from designers to operators, from practical engineers to executives, that is effective risk reduction activities can be realized by all members efforts in the plant.
Hiroshi Ujita, Naoko Matsuo
Open Access
Article
Conference Proceedings
3 sprints from zero to innovative medical device in 16 months: Benefits of combining Human Factors and Agile
This study aims to lay out an Agile product development case study-oriented research with core tenets on the process mapping and the methodologies involved in the solution implementation. The developed prototype is used for measuring the principal vital signs, without contact, only through video images. The measured vital signs are heart rate, respiratory rate, oxygen saturation, temperature, and blood pressure contactless at 2 meters (6.5 ft). The developed solution was presented in the framework of public bidding for the emergency service of the autonomous community of Andalucía (in Spain). The Agile project management approach has been integrated to overcome the limitations of medical devices' commonly accepted Stage-Gate project management approach. During the prototype's concept and detailed design phases, eight designs for Usability (DfU) tools were implemented to generate value. These tools were implemented in the concept phase in parallel with developing the IP strategy, contextual research, risk management strategy, and regulatory strategy development to identify the user's needs in an iterative process. The users in this case study were paramedics, EMT’s and EMC’s. Further, during the detailed design phase, the DfU helped detect design flaws and usability issues before the validation phase. A multifunctional team of eight specialists was consolidated to develop the solution, with role distribution according to the scrum team model. This team has been working together for 16 months. In the last sprint, first responders tested the prototype with a TRL 7 in laboratory and field trials simulating real conditions. The results were collected through several requirement acquisition techniques. The prototype was continuously improved by collecting value-generating data along the project and establishing strategic checkpoints. Thus, many design flaws and usability issues were prevented throughout the concept and development phase. Besides, reducing the development time without compromising all the necessary design traceability and quality requirements according to ISO 13485 standards
Adrian Morales Casas, Amparo López Vicente, Lorenzo Solano-García, Jose Laparra
Open Access
Article
Conference Proceedings
Developing a Quality Control System for Biotechnological Device Inspection Improvement
Incoming quality control (IQC) is integral to quality management system of manufacturing industries. IQC plays a significant role in ensuring delivery of high standard products to the target customers and, in turn, affects the company’s reputation and their competitiveness in the industry. Presenting a case from a biotechnology company, the purpose of this research is to develop a quality control system for inspection improvement of a biotechnological device. During the COVID-19 pandemic, the IQC Department encountered inconsistencies with output rate when providing inspected parts to the Manufacturing Department: an issue that could be mitigated with a documented process that addresses the prevalent issues that plague the current unestablished IQC system. This study utilized the Lean Six Sigma Methodology to achieve improvement for the IQC Department practice for enhanced performance by identifying root causes of inconsistencies, and creating a systematic documented process for IQC department. Upon successful analysis and implementation of the new IQC inspecting system, the non-value-added time decreased by over fifty percent. While this project is the first stepping stone in improving the IQC Department, its significant results emphasizes the integral contribution of quality control and Six Sigma practices in creating a continuous improvement system which ensures consistent high-quality instruments are being produced for the customers.
Harsimran Hothi, Fatemeh Davoudi Kakhki
Open Access
Article
Conference Proceedings
Empirical Study of Machine Learning for Intelligent Bearing Fault Diagnosis
Bearing failure highly impacts performance and production of manufacturing systems, causes safety incidents, and results in casualties and property loss. According to the current literature, bearing faults cause 30-40% of all failures in induction motors. Therefore, identification of bearing faults, at early stages, is crucial to ensure seamless and reliable operation of induction motors in industrial and manufacturing operations. Faults occur in four components of bearing: inner race, outer race, ball, and cage. Regardless of the component in which fault occurs, it causes changes in vibration signals. Therefore, comparing normal signals with faulty ones is helpful in detecting localized faults in bearings. We use a benchmark publicly-available data set to conduct this analysis. The main challenge in using publicly-available benchmark datasets for fault detection is lack of manual for instruction on analysis experiments on the original data, which leaves researchers with the challenge and opportunity of applying various analytical methods for achieving higher accuracy rates and useful models for fault detection. This study presents a machine learning-based fault detection and classification scheme in induction motors to evaluate the significance and effects of various data preparation and feature extraction methods on accuracy and reliability of fault detection outcomes. The data preparation stage includes discussion of efficient data dimension reduction, and noise eradication, as well as feature extraction methods for induction motor signals. The main methodology is developing a variety of machine learning classifiers for detection and classification of normal bearings versus faulty bearings. Finally, the implications of the methodology and results for early fault diagnosis and enhanced reliability, as well as maintenance planning efforts in manufacturing systems are discussed. This study introduces proper implementation of machine learning models to improve system performance with higher speed and reliability. Furthermore, the methodology and results contribute to planning and undertaking maintenance operation more efficiently. Therefore, the approach, methodology, and results will be beneficial to both researchers and practitioners involved in manufacturing systems reliability analysis and optimization.
Armin Moghadam, Fatemeh Davoudi Kakhki
Open Access
Article
Conference Proceedings
Estimation of relative standard deviation related to limit of detection and limit of quantitation
Limit of detection (LOD) is usually determined by calculation of the standard deviation of measurements of blank samples. In several technical reports, LOD is defined as the concentration at the relative standard deviation (RSD) 30% (or other values) for repeated measurements. Similarly, limit of quantitation (LOQ) is also defined at the RSD level 10%. When a laboratory starts to use a method, the method verification should be carried out in advance to guarantee this method can be implemented correctly and the method characteristics (eg. LOD and LOQ) can be satisfied in this lab. But in routine test, this verification is not conducted every time and the measurement result might be effected by several factors. Then the verification results can vary under different test conditions. In this article the critical value of relative standard deviation is presented, when the RSD from routine test of blank samples of n times larger than the critical value it can be concluded that this measurement system cannot meet the requirement of LOD/LOQ that defined by the methods related with RSD. This method shows a quick check whether the routine measurement can satisfy the defined LOD/LOQ.
Fan Zhang, Jing Zhao, Xuan Zhang
Open Access
Article
Conference Proceedings
Comparison of consumer’s risk quality for different sampling plan corresponding to adjacent sample size
In some practical cases, people want to know the risk difference of the sampling plan corresponding to adjacent sample sizes. This paper mainly discusses the difference of consumer’s risk quality for different sampling plan for both the sampling procedures for inspection by attributes and by variables with adjacent sample sizes. What’s more, we gave the analysis of consumer’s risk quality in different lot size and sample size. The results show that in the sampling procedures for inspection by attributes the exact lot size within the same lot range has little effect to the consumer’s risk quality. The key factor affecting the acceptance probability is the acceptance number. In the sam-pling procedures for inspection by variables, as the sample size increases, the consum-er’s risk quality decreases.
Jing Zhao, Xuan Zhang, Fan Zhang, Gang Wu
Open Access
Article
Conference Proceedings
Harmonizing the graduate attributes of mechanical and industrial engineering with the Fourth Industrial Revolution needs in automotive production
Significant global shifts have inundated the production of automotive components over the past few years. To meet global "Sustainable Development Goals," the industry is moving from internal combustion engines to electric vehicles. The fourth industrial revolution has changed the current phase of global manufacturing's competitiveness and can potentially increase competitiveness in the future. Because of this shift, manufacturers of automotive components now need different skill sets. Consequently, a better alignment of graduate attributes with evolving industry demands is necessary to create sustainable job opportunities for industrial and mechanical engineering graduates expected to fill critical roles in the automotive manufacturing industry. This paper presents the findings of an investigation into the engineering programs of higher education institutions within South Africa and how the engineering graduate attributes in the mechanical and industrial programs align with the automotive industry demands. The advent of the Fourth Industrial Revolution has caused significant upheaval in employment stability. Apprentices are being phased out of the workforce and replaced by smart machines. The automobile industry has seen revolutionary changes in its production methods in the last century. Conversely, higher institutions have not implemented major curriculum changes and still practice traditional teaching processes. The technology used in the average classroom has barely changed in the past three to four decades. The study's overarching goal was to create a model that colleges and universities can use to close the skills gaps through curriculum updates that better prepare students for success in the workplace. The automotive sector and academic institutions collaborated on an action research project to develop this framework. A framework emerged from the study aimed at assessing how well higher education institutions meet the needs of industries, and it shows the required measures to remain competitive.
Timothy Laseinde
Open Access
Article
Conference Proceedings
Factors Influencing Globalization of Logistics Management in Nigeria
Companies in the developed world operates easily in the global market because the factors that influence globalization of logistics management have been studied and the elements influencing globalization have made the process flexible and accommodating. But little is known about the factors that influence globalization of logistics management in Nigeria. Therefore, this study set out to determine the various factors that could influence globalization of logistics management in Nigeria. The study adopted a quantitative approach through the use of a questionnaire survey carried out among selected professionals and consultants in operations, logistics and supply chain department of companies within Lagos, Nigeria. Data gathered were analysed using percentages, mean item score and factor analysis. The research instrument reliability was verified using Cronbach alpha test while the factorability of the data collected was tested using the Kaiser-Meyer-Olkin measure of sampling adequacy and Bartlett's Test of Sphericity. The result revealed that the three cluster factors that influence globalization of logistics management in Nigeria are political, cultural, and economic which were ranked highest. The findings also revealed that all respondents have similar views on the factors that influence globalization in Nigeria. Lastly, since the respondents have agreed that the factors listed influence globalization of logistics management, it is therefore necessary for the Nigerian government and stakeholders in logistics management to look into these factors as a way of closely integrating markets, economies, societies, and ensuring more products are available to consumers universally.
Ayodeji Dennis Adeitan, Clinton Aigbavboa, Oyindamola Cynthia Olubiyo
Open Access
Article
Conference Proceedings
Optimization of Machined Product Quality in The Milling Process of Inconel High-Tech Material
Today, Inconel 601 materials are used in special areas and frequently processed in the aerospace industry. Due to the high specific expectation of sectors, the manufacturing quality of Inconel 601 material is crucial. There are some studies in the literature related to the optimization of milling process parameters such as cutting speed, feed rate, and depth of cut to reach high-quality characteristics depending on the quality expectations. We aimed to optimize the surface roughness, manufacturing lead time, and energy consumption that will occur during the milling process of the Inconel 601 workpiece. Spindle speed, depth of cut, and feed rate of the cutting tool parameters and their levels are used as parameters (factors) in the design of the experimental study. Then the ANOVA tables are obtained. Furthermore, regression equations of the quality characteristics are determined. Finally, a multi-response optimization study is proposed to optimize parameter levels considering to achieve the maximum quality level of the machined part.
Yusuf Tansel Ic, Zeki Anıl Adıgüzel, Baran Azizoğlu, Alparslan Eren Keskin, Minesu Köksal, Berat Subutay Özbek
Open Access
Article
Conference Proceedings
Analyzing The Effects of Human Resource Allocation and Learning by Experience on Project Management in Defense Industry
Activities that started using various resources and carried out to produce a product or service in a limited time are called projects. Process of delivering the project to an end with plans made to achieve project's goals in desired extent and time is called project management. Successful project management is becoming more important for competing companies. The project manager, who is responsible for execution of one or more projects, gains a lot of experience throughout the process and becomes more knowledgeable and skilled. The main purpose of this study is to reveal the effects of learning with experience and human resources allocation on multi-project management. Survey which is prepared to evaluate the sub-goals under the main purpose is applied online to the project managers who are working in institutions operating in defense industry in Ankara. Data obtained via the survey are analyzed by a statistical software. As a result, it’s found that the current knowledge of employees and their experience have a positive effect on managing projects. It’s been evaluated that there may be disruptions in customer relations and project management when human resource planning is insufficient and it’s important to consider the experience of employees to make allocations.
Baris Kececi, Melis Colak
Open Access
Article
Conference Proceedings
Determination of preferences in auto glass selection process
Glass is a solid material with an inorganic amorphous structure, prone to fracture, defined as transparent or translucent, and usually observed in a complicated form. In auto glasses, on the other hand, transparency, that is, light transmittance is directly proportional to the colour of the glass. In auto windows, the colour of the glass is of great importance because the driver's vision is crucial due to specific light transmission rules. However, the thickness of the auto glass characterized as durable also causes different preferences in terms of customer requests. In this study, we carried out to rank the customer preferences based on customer expectations using the sales data for three years in terms of the colour and thickness of auto glass. Within the scope of the study, we proposed a trapezoidal fuzzy number integrated fuzzy entropy and fuzzy TOPSIS model to rank the alternative auto glass. A case study is also presented for illustrative purposes.
Kumru Didem Atalay, Yusuf Tansel Ic
Open Access
Article
Conference Proceedings
After-Sales Obsolescence Risk Management In Long-Life Defense Projects
In the defense industry, products are often complex systems developed and maintained with detailed and complex business processes. In such systems, management and planning are difficult and complex in cases such as parts supply or production. The end-of-life phase of products is the final stage of the product lifecycle, which begins with product retirement and ends with the expiration of all service contracts. Obsolescence will occur at the end of its useful life, where remanufacturing used or obsolete products can be an alternative source of obtaining spare parts. For this reason, the proper methods should be selected and applied for each stage. This study proposes an obsolescence management model of critical materials to be determined in a large-scale defense industry company. The model aims to reduce the adverse effects of problems throughout the life cycle of products and also to eliminate existing communication and integration deficiencies in processes. With this model, outputs such as purchasing a sufficient number of products to meet the system's requirements during its predicted life, minimizing the cost by optimizing the process, and maximizing the availability of spare parts have been achieved.
Esra Dinler, Ceren Karagoz Kati
Open Access
Article
Conference Proceedings
A Conceptualised Rescheduling Approach to Minimise Manufacturing Disruptions in the South African Automotive Industry.
Manufacturing organisations are very important industry globally as the goods that are produced and supply for fills the day to day demand of customers and any disruption within the manufacturing sub system, can be very detrimental to the organisation, as it will create a bottleneck that can put a constraint to the entire system and render it obsolete, particularly as observed from the South African automotive industry, using a number of productivity, reliability and failure techniques. According to the results, it shows that manufacturing disruption can be minimized if the proper reliability strategies and rescheduling models are put in place.
John M Ikome, Opeyeolu Timothy Laseinde
Open Access
Article
Conference Proceedings
An Analysis of the South African Automotive Industry Local Content as an Approach to Global Competitiveness
This paper attempt to analyse the global competitiveness of the South African automotive industry with a major focus of it local content and importation of automotive components, a well-structured questionnaire was developed after a careful literature review and administered in the case studies automotive industries, the analysis indicates that importation of cheap automotive components have a negatively impact on the South African automotive industry and proper control of importation will be a possible solution for a well balance and competitive improvement for the South African automotive industry.
John M Ikome, Opeyeolu Timothy Laseinde
Open Access
Article
Conference Proceedings
A Dynamic Approach to Minimise Bottlenecks and Improve manufacturing competitiveness in a case study manufacturing Industry.
Manufacturing organisations are key to the well-being of the society and the combination of competitiveness forces including modern technology adaptation is of great importance in order to obtain the goal of competitive improvement, particularly in a conflicted supply chain system during the production process, a number of manufacturing constraints were identified using the theory of constraint, namely, machine breakdown,employees absenteeism and power failure
John M Ikome
Open Access
Article
Conference Proceedings
Collaborative Initiatives: An information-sharing approach in retail drop shipping supply chain
Retail dropshipping has become increasingly popular due to its ability to reduce inventory holding costs and enhance customer satisfaction. This model involves retailers displaying goods online and sending customer data to producers who ship directly to customers. However, this approach impedes scalability, such as poor communication among supply chain partners and a lack of inventory transparency. This research paper proposes a collaborative initiative that utilizes information sharing to improve the efficiency and effectiveness of the retail dropshipping supply chain. Sharing downstream sales data with upstream partners can significantly enhance inventory visibility, reduce order fulfillment time, and improve communication and coordination among supply chain partners. Indepth literature review was conducted to identify relevant articles and studies on collaboration in the supply chain, information sharing, and dropshipping. The study revealed the potential benefits of collaborative initiatives and emphasized how information sharing can help overcome some of the limitations of the conventional dropshipping model. The research provides valuable insights into collaborative initiatives in the retail dropshipping supply chain and highlights the crucial role of information sharing in enhancing supply chain operations. By adopting joint initiatives, retailers can overcome the constraints of the traditional dropshipping model and increase profitability. Our study offers a framework for retailers and supply chain partners to collaborate effectively and improve the efficiency and effectiveness of their operations.
Oluwaseun Laseinde, Clinton Aigbavboa
Open Access
Article
Conference Proceedings
Exploring the effectiveness of Collaborative Planning, Forecasting and Replenishment (CPFR) in enhancing supply chain performance in drop shipping
Business operations have shifted from inter-organization to cross-enterprise due to supply chain management improvements and information technology advancements. New business models have emerged in response to the explosive growth of online retail, including the drop-shipping concept. Dropshipping is a relatively new type of order fulfillment in which the retailer does not store inventory. The merchant displays goods online and sends customer data to the producer, who ships straight to the customer. This method is frequently utilized as a supply chain solution to meet online demand. However, this model faces several challenges, such as uncertainty of demand, lack of control over inventory, and the need for efficient collaboration with suppliers. This paper explores the effectiveness of Collaborative Planning, Forecasting, and Replenishment (CPFR) in enhancing supply chain performance in dropshipping. Relevant literature on CPFR and drop shipping were explored and the findings indicate that CPFR is an effective strategy for improving supply chain performance in dropshipping. By enhancing collaboration and communication between suppliers and sellers, CPFR helps to mitigate the challenges faced by the dropshipping model.
Oluwaseun Laseinde, Clinton Aigbavboa
Open Access
Article
Conference Proceedings