Production Management and Process Control
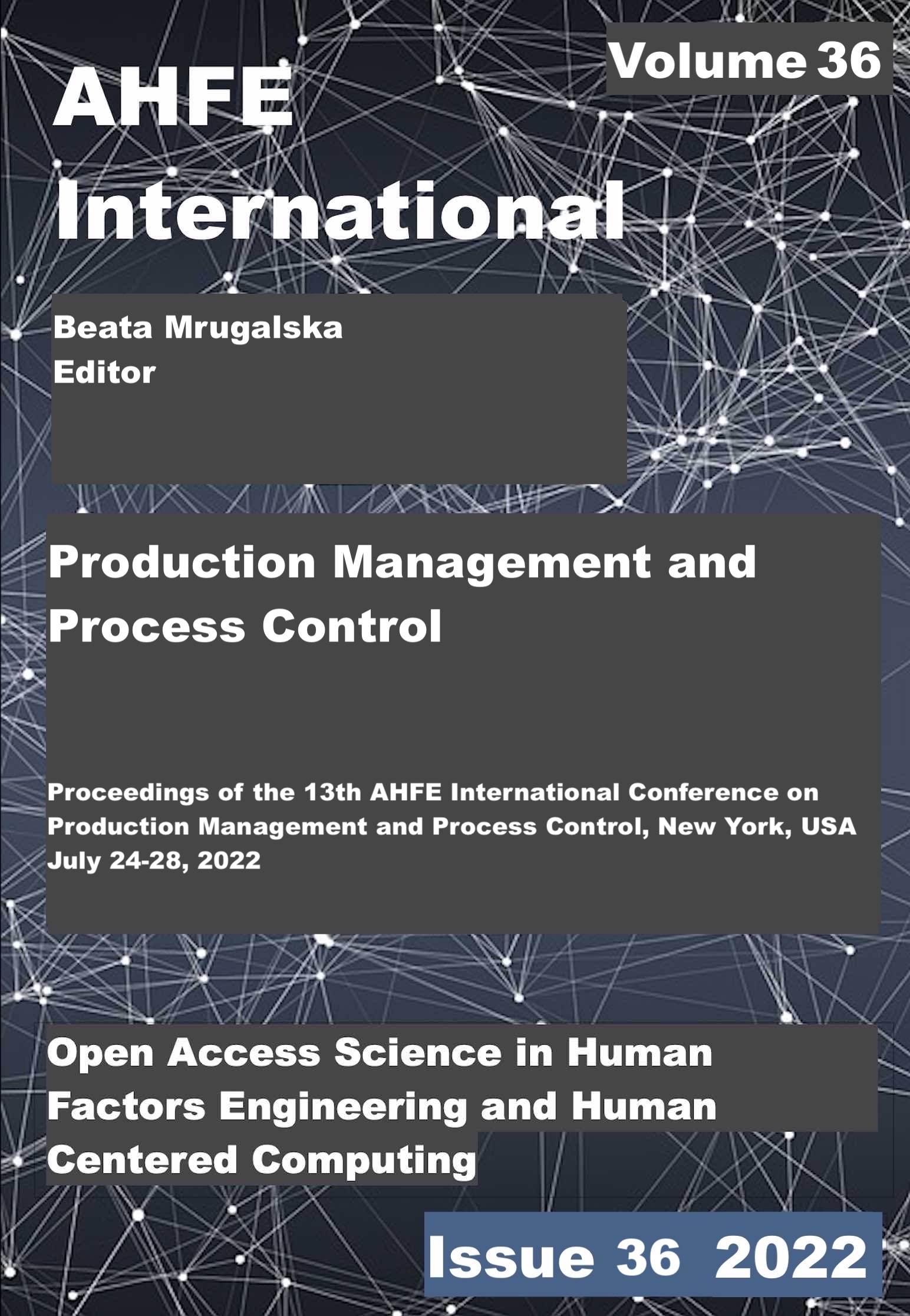
Editors: Beata Mrugalska
Topics: Production Management and Process Control
Publication Date: 2022
ISBN: 978-1-958651-12-4
DOI: 10.54941/ahfe1001612
Articles
Augmented Reality-based Programming of Robot Arms
Programming of production systems depends on highly specialized personnel and proprietary development environments. This can hinder the evolution towards flexible production. In this paper we present a concept for an intuitive way of human-machine interaction by utilizing the augmented reality technology. This involves a method of programming a machine using an augmented reality headset. All desired machine operations can be predefined via a virtual user interface and by arbitrary placement of virtual working points. We further show how the referencing of the coordinate systems of the augmented reality environment and the robot can be accomplished. We prototypically apply the concept to a robotic arm with 6 degrees of freedom and employ a Microsoft HoloLens 2 optical head-mounted display to interact with robotic arm in the virtual world.
Vladimir Kutscher, David Bassauer, Thomas Dasbach, Reiner Anderl
Open Access
Article
Conference Proceedings
Configuration of a Web-Based Digital Twin using a Modular and Flexible Simulation Chain
The versatile concept of the digital twin is being applied in various economic sectors. To exploit its full potential, the digital twin has to be adaptable to changing requirements. In this paper we address the configuration of digital twins with a focus on a flexible and modular simulation chain. Thereby, we utilize the Functional Mock-Up Interface to enable variable configurations based on basic simulation components. We validate the concept by a prototypical implementation.
Christian Plesker, Vladimir Kutscher, David Bassauer, Reiner Anderl
Open Access
Article
Conference Proceedings
Medical Devices Analysed from the Human Factors and Ergonomics in Engineering Design Point of View: Case Study
Here two real case studies of design and development with different grades of complexity are presented. A medical instrument prototype of a pneumatic retraction and holding system for surgical procedures and an electromedical device for non-invasive glucose measuring developed both from a TRL 4 to reach a TRL 7. The products were designed in the frame time of six months and fifteen months, respectively. The medical instrument was developed using a conventional Lean project and engineering design approach. Meanwhile, the electromedical device was created using Lean project management alongside a human-centred design and person-oriented innovation approaches. Based on the Lean approach, both products were built on a common ground project development path that the IBV follows. Besides, both projects had a common limiting factor, the need to meet a very demanding schedule of deadlines. The paper details the development stages followed in both products to compare how the human-centred design methods are integrated and could have been incorporated in the medical instrument case. Based on the Institute of Biomechanics’ (IBV) background in project management in the design, development and innovation of medical devices, this paper seeks to share applied knowledge on successfully implementing human factors plan and ergonomics in the engineering design process.
Adrian Morales Casas, Jose Laparra, Nicolás Palomares, Carlos Atienza, Lorenzo Solano-García
Open Access
Article
Conference Proceedings
The South African Automotive Industry’s Competitiveness and Supply Chain Integration Challenges.
The South African automotive industry Supply Chain Management is a very important element and plays a key role in its competitiveness. According to the survey and results, it shows that high operational cost, including customer’s cancellations, power failure and cheap imports are a major concern to its global competitiveness. As a result, the development of good competitive Supply Chain Strategies if vital.
John M Ikome, Timothy Laseinde, Grace M Kanakana Katumba
Open Access
Article
Conference Proceedings
The Competitive and Productivity Challenges in developing nations: a case study of South African Automotive Industry
The South African automotive industry is a key player to the economic growth of the nation and due to the global competitiveness, it is facing a lot of pressure. After the application of productivity methodology which a very important tool in measuring the efficiency of a system, it is evident that more still need to be done in order for this industry to be globally competitive within the constantly changing customers demand.
John M Ikome, Timothy Laseinde, Grace M Kanakana Katumba
Open Access
Article
Conference Proceedings
Barriers for implementing reverse logistics in South African construction organizations
this papers aims to present a survey of the perception of the barriers to implementing reverse logistics practices in South African construction organisations. Despite the extensive research on forward logistics and RL, there is a paucity of studies that examine the barriers to implementing RL particularly within the South African construction industry that hinders the implementation of RL. Data were collected by utilising the use of questionnaires. The quantitative survey data were subjected to descriptive analysis. The following barriers were indicated as most significant; lack of awareness of reverse logistics practices, lack of knowledge of the revenue reverse logistics brings. The least ranked barriers are limited forecasting and planning in reverse logistics, lack of pressure from community and perceived idea that the cost of adopting RL is high. First, the reported findings are focussed on one study that used questionnaire surveys within the construction industry; therefore, the results may not be generalisable to other contexts. The barriers identified could be used as a road map for the development of appropiate solutions for the successful implementation of RL.
Unathi Makalima, Clinton Aigbavboa, Ifije Ohiomah, Nita Sukdeo
Open Access
Article
Conference Proceedings
Development of a Guideline for the Sensor Layout Plan
With the increasing relevance of Industry 4.0 and the associated data-based processes, efficient and structured data collection is becoming increasingly important. Currently, sensors are used in a large majority of industries to enable automation processes and to check product quality. The collected data is evaluated directly in the plant to control processes. Apart from this, other production and usage data are in most cases either not collected at all or not collected in a targeted manner. This is because manufacturing companies are often more focused on the purely functional aspects of a plant and attach too little importance to the potential of data.However, the targeted collection and processing of data will become increasingly important in the future. Some application examples of this are the digital twin, condition monitoring, predictive maintenance or remote access. These applications can significantly optimize industrial production processes concerning the three most important factors of time, cost and quality. The basis of these and other applications is data that must be collected, transmitted and processed in a targeted manner. The aspect of targeting is important so that no relevant data is missing for the intended purposes and sensors have to be retrofitted at great expense. With a view to sustainability, on the other hand, unnecessary data should not be transmitted and stored, so that networks and databases are not unnecessarily burdened.To be able to collect data purposefully, appropriate sensors must be available. Since the retrofitting of such sensors is complex, expensive and sometimes not possible afterwards, the type, number and position of the necessary sensors should already be considered during product and system development. Since there is currently no standardized procedure regarding efficient sensor planning for the development department, it's necessary to develop a guideline for this area that supports the employees. The result of this development on the one hand is the guideline, which suggests and accompanies an efficient procedure for sensor planning. On the other hand, it is the Sensor Layout Plan (SLP) itself, which as a standardized document focuses on the sensor technology in products and plants and maps all relevant information in a holistic approach.The guideline for the SLP is based on a structured approach. It includes a holistic analysis of sensor needs and a model-based methodology for planning sensor selection and placement in products or plants. First step in creating an SLP according to the developed guideline is to analyze the required data and planned data usage. The company's business model plays a primary role. In the second step, the current actual and currently possible data collection is analyzed. Then the selection of the required instruments for data collection takes place. Besides sensors, calculations, for example based on artificial intelligence, or simulations are also possible. After the selection of the sensor technology, the placement and positioning are considered in the hardware and in the software. The topic of data storage and management is considered conclusively.
Tanja Steinbach, Benjamin Roehm, Reiner Anderl
Open Access
Article
Conference Proceedings
Multimodal Human Systems Exploration with Tangible XR for the Internet of Production: An expert survey
Agile product development makes it possible to react flexibly to changing customer requirements. In this context, user and expert assessments, explorations and tests are very important, since customer requirements can often be easier identified by testing a first product or a prototype. Due to complex and long development processes, the development of prototypes is often time-consuming and costly. To improve this, we are developing a method in which the use of mixed reality (XR) allows certain product functionalities to be explored at a very early stage by using multimodal virtual prototypes. Traditional virtual reality (VR) addresses only the visual and acoustic modalities and is limited in its immersion, which is especially impeding for products where physical interaction and haptic experience is an important part of the product functionalities. Based on the findings of the multiple resources theory, Tangible XR allows part of this haptic experience to be experienced and integrated with the virtual experience, so that change requests to the product based on user or expert assessments can be identified and implemented at an early stage of the development process of socio-technical systems. In addition to this retrospective user assessment, Tangible XR can also be used to prospectively explore and develop product functionalities in an exploratory manner together with stakeholders. This exploratory paradigm can be an essential component of agile processes. The explorative approach developed is presented by using a Tangible XR car door opening mechanism as a demonstrator. Based on an expert study, a first proof of concept is presented.
Michael Preutenborbeck, Marcel Usai, Nicolas Herzberger, Frank Flemisch
Open Access
Article
Conference Proceedings
A Domain-independent Model for KPI-based Process Management
Monitoring, assessing, and improving company processes is one of the most important and challenging tasks of management. Key Performance Indicators (KPIs) are a well-established means of assessing and managing company processes and performance. In previous publications, we transferred the concept of KPIs to mechatronic products. Here KPIs are calculated based on data generated within the production process. Thus, the KPIs provide information about the current condition of the production process and produced products and enable efficient product and process control. The basis of this approach is a KPI model, which enables the specification of company-specific products, product-specific KPIs, and limits. By structuring the KPIs as a hierarchical system, company goals can be expressed at different levels of abstraction through the KPIs and their limits. Thus, goals are assessable for stakeholders at all management levels, which eases communication and reporting. Furthermore, the hierarchical approach allows for a high degree of transparency regarding the monitored processes and potential bottlenecks. Underperforming KPIs can be explained in more detail by diving into subordinated KPIs, utilizing the provided hierarchy. In this paper, we present a revised, domain-independent version of our KPI model. The revised model allows the definition of company-specific processes, products, and data sources that can be linked to the KPIs. In addition, mechanisms have been implemented to add additional parallel or hierarchical company-related levels, such as teams or company sites. To illustrate this, we show the application of the model in two different domains: Supply chain management and software development. For supply chain management, we consider the supply of parts in the material procurement of a manufacturing company. To ensure smooth production, it is essential that the right components are available and, thus, the so-called Seven-Rights of logistics are guaranteed. At the same time, high availability with other target variables is tangential to high logistical efficiency in a company's procurement and production. In this paper, the component availability is considered as top-level KPI, which consists of subordinated KPIs such as the delivery quantity reliability or the delivery time announced by the supplier. Thus, increased component availability can be achieved and further information, such as supplier quality, can be derived and utilized.For software development, we utilize the KPI model to assess and guide a company's DevOps transformation. DevOps was inspired by agile approaches to manage and improve production processes, such as Lean or the Toyota Way. The DevOps transformation is difficult for most companies, as each company may have different reasons and goals associated with it. Some companies aim to increase their software deployment rate, while others focus on software stability and quality. To support companies with this complex task of changing their development process, as well as parts of their organization's culture, a flexible and unique model is needed. In our example, a DevOps maturity index, based on performance, quality, and organizational KPIs is introduced using our KPI model. Based on this index, the status of the DevOps transformation is monitored and the next steps for the transformation can be derived.
Benedict Wohlers, Jan Strüwer, Felix Schreckenberg, Felix Barczewicz, Stefan Dziwok
Open Access
Article
Conference Proceedings
The influence of ergonomics as a quality parameter on the evaluation of manual assembly processes
Current trends in the development of automation and digitalization of production processes allow new approaches to data collection and processing. The development of technology and the speed of change mean that companies are not always able to take advantage of the benefits of applying these modern possibilities. New tools make it possible to increase the efficiency of manufacturing processes while at the same time optimizing them. Various classical methodologies for evaluating production processes are used for this purpose. However, these methodologies often fail to respond to the development of the industry and are not sufficient for objective evaluation of production processes. A significant shortcoming is the difficulty of standardizing the general analysis of the production process or of including qualitative evaluation parameters among the quantitative ones. This is reflected in inaccurate evaluation outputs, especially in the manual processes of larger assembly units with a high proportion of human labor. Due to the higher proportion of human labor, errors and shortcomings often occur in these processes, which can be linked precisely to qualitative parameters that cannot be easily determined from the database of quantitative parameters.One such parameter is the ergonomics of the tasks performed, particularly in terms of inappropriate working positions. The identification of these parameters and their influence on the evaluation of production processes is critical for the competitiveness of manufacturing companies. The development of modern technologies, specifically Motion Capture suits, allows these parameters to be monitored, recorded, evaluated, and subsequently included in a comprehensive evaluation of manufacturing processes. Motion Capture technology enables the recording of working motion and ranges of limb angles relative to a specified plane of the person being measured at any given time. Work movements are recorded in real-time and the resulting data can then be processed and evaluated. This data in the form of qualitative indicators are used to support and objectify the evaluation of production processes. The approach allows for higher evaluation accuracy and helps manufacturing companies optimize other business processes to ensure greater competitiveness. This paper deals specifically with the process of using the Motion Capture suit to identify quality parameters for the evaluation of manufacturing processes.
Filip Rybnikár, Michal Šimon, Pavel Vránek, Ilona Kačerová
Open Access
Article
Conference Proceedings
Project Planning: A Determinant of Project Delivery to Time and Cost
Planning is not only the most basic of all the managerial functions, it also determines how the other functions will be implemented. With efficient project planning, utilisation of administrations, and hierarchical strategies, proper project operations can be sequenced to achieve a successful project delivery. This research study set out to appraise the project planning impact on project delivery. To achieve this, a qualitative research method was adopted in which archival data was obtained for public building projects executed between January and December 2021 within Lagos State, Nigeria. Analysis of retrieved data was done using descriptive statistics and Pearson Correlation. The findings indicated that a significant relationship exists between time overrun and cost overrun while planning techniques used for projects has a non-linear relationship with time and cost overrun experienced on construction projects. The study concluded that planning plays a major role in the successful delivery of construction projects. Hence, there is a need to incorporate adequate project planning into the pre-contract phase activities on construction projects.
Opeoluwa Akinradewo, Clinton Aigbavboa, Matthew Ikuabe, Peter Adekunle, Wellington Didibhuku Thwala, Shola Olatunji
Open Access
Article
Conference Proceedings
Construction Project Planning Techniques: Awareness, Usage and Suitability
Every project is unique on its own with predetermined commencement and delivery dates. The constraints imposed on the project make it necessary to plan its execution to keep it within those constraints. The checks and balances put in place in the construction industry to facilitate the completion of projects within the contractor’s schedule and to the client’s desired time, quality and cost as planning techniques are applied in varying degrees depending on the stage at which it is carried out. The main purpose of this study is to evaluate the various construction project planning techniques employed in the Nigerian construction industry and the suitability of these techniques. To achieve the objectives of the study, a quantitative research method was utilised and a well-structured questionnaire was contrived using variables obtained from reviewed literature. The respondents chosen are Quantity Surveyors, Builders, Engineers, and Architects. Analysis of retrieved data was done using Percentile, Frequency, Mean Item Score (MIS). Findings of the study revealed that Bar/Gantt chart is the widely used planning technique as it is efficient while the Critical Path Method is more accurate in ensuring a project is delivered to the scheduled time and predetermined cost. From the result of this study, it is concluded that awareness level and recognition of planning techniques in the Nigerian construction industry is low and proper project planning is seldomly practised which requires urgent professional attention. This will help in ensuring that construction project time and cost overrun are addressed from the commencement of the project.
Opeoluwa Akinradewo, Clinton Aigbavboa, Babatunde Fatai Ogunbayo, Didi Thwala, Ornella Tanga, Olushola Akinradewo
Open Access
Article
Conference Proceedings
Dynamic Scheduling Techniques in Cloud Manufacturing – An Exploration of Deep Reinforcement Learning as a Critical Opportunity for Future Research
Objective: Determine the state-of-the-art in dynamic scheduling techniques for cloud manufacturing.Significance: This paper firmly establishes the underexplored technique of Deep Reinforcement Learning as the state-of-the-art for dynamic scheduling in cloud manufacturing, exposes a significant gap in the literature, and sets out critical future research objectives.Abstract:For many years, metaheuristic algorithms have represented the state of the art in manufacturing scheduling techniques, proving to be exceptionally reliable for optimising schedules. However, metaheuristics suffer from inherent weaknesses that inhibit their ability to be applied to dynamic cloud manufacturing (CMfg) scheduling problems in practice. Thanks to the very recent and rapidly accelerating development in deep reinforcement learning (DRL), a small sample of studies have described how those approaches have thoroughly outperformed metaheuristic algorithms in dynamic manufacturing scheduling problems, establishing a new state of the art. However, a significant lag in maturity exists between the algorithms used in CMfg and state-of-the-art DRL. This paper systematically reviews the CMfg scheduling literature published between 2010 and 2020, summarises the development of deep reinforcement learning in this context and offers valuable directions for future research.
David Chambers, Thorsten Lammers, Kun Yu
Open Access
Article
Conference Proceedings
Product Data Quality in e-Commerce: Key Success Factors and Challenges
This paper discusses basic attributes which are entered to product data in selected e-commerce platforms. For this aim, we selected and analyzed a group of attributes such brand name, product image, net content, product classification and sale country. We also reviewed the platform developers which are commonly used in e-commerce. It allowed us to provide their best practices. Furthermore, for each of the selected product attributes, an analysis was carried out in reference to presence, mandatory field and data input validators. The research results point out inconsistencies in the basic attributes of the product which lead to low product quality data. The lack of commonly available and standardized data, which could describe products, makes manufacturers create own recommendations for the e-commerce market. Furthermore, they even generate and develop their own meaning of some data. Therefore, it is urgent to undertake steps to be able to recognize correctly e-product data as this market is still new one. On the other hand, the meaning of e-product data can be greater or even different in comparison to a traditional trade. This paper provides recommendations for managers of e-commerce platforms how to cope with e-product data using a single standard for product master data and common product identifier to increase quality of e-product data.
Maciej Niemir, Beata Mrugalska
Open Access
Article
Conference Proceedings
Optical Diagnostics of the Dispersion Composition of Fuel-Air Flare
One of the central problems of using heavy hydrocarbons as fuel for thermal burners and internal combustion engines is mixture formation. The purpose of this article is to present the results of optical diagnostics of the dispersion composition of a fuel-air torch according to the developed method. The technical means of the information acquisition and processing system can be a high-speed micropyrometric complex for measuring temperature and flame propagation velocity, the main elements of which are a personal computer and a VideoSprint high-speed video camera. The software includes the Origin data analysis package and ImageJ, a free image processing program. The peculiarity of the video camera is that it can detect low-intensity radiation due to amplification in microchannel plates, and the speed and multi-frame exposure is provided by an electronic shutter. To use video cameras as high-speed pyrometers, their preliminary calibration is necessary. During the calibration of the video camera, the non-linearity of the response of the measuring system depending on the exposure time was revealed. The study of the injection process in diesel mixture formation requires reliable information on the relationship between the speed characteristics of the fuel jet and the dynamics of the fuel supply cycle. Optical research methods do not destroy the structure of the fuel plume and allow obtaining information about the structure and dynamics of the flame development. The technique also makes it possible to obtain data on the root angles of fuel plumes and to estimate the distribution of aerosol particles along their length. For analysis, an experimental frame of the fuel atomization process was taken, made in the Videoscan VS-SST-285 system with an exposure of 39 µs, the delay time of the sync pulse from the pressure sensor was 300 µs. From the analysis of the fuel jet, it was found that the maximum fuel concentration is observed at the atomizer, in the initial zone of the jet and in the front (less than at the atomizer), and there is also a deviation of the torch core axis from the nozzle axis. As experiments show, a change in the angle of the spray cone by 10° and a deviation of the axis of the cone from the axis of the nozzle are permissible by 3-5°. Obtaining data for processing using a high-speed micropyrometric complex can greatly improve the quality of diagnostics. The result of experimental data processing according to the proposed method is consistent with the previously obtained results, which indicates great prospects for further development of this express diagnostic method to obtain numerical characteristics of fuel jet dispersity and improve the ecology of heavy hydrocarbon combustion processes.
Oksana Isaeva, Marina Boronenko, Yura Boronenko
Open Access
Article
Conference Proceedings
Measuring the Velocity and Temperature of Particles in a Low-Temperature Plasma Flow
The improvement of optical methods for diagnosing fast processes in plasma deposition technologies is associated with the solution of a well-known contradiction between an increase in the speed of recording a track of a moving particle and a decrease in the signal level to a critical noise threshold. Improving the accuracy of measuring the temperature of the condensed phase of the flow, under the conditions of plasma background radiation, is possible with the transition from the brightness pyrometry of individual particles to spectral methods for determining the temperature distribution of a large group of particles by their thermal spectrum. The purpose of this study is to experimentally verify the effectiveness of using microchannel photomultipliers and nanosecond electron-optical switches to improve the accuracy and speed of time-of-flight anemometry and brightness pyrometry methods. The experimental technique for detecting tracks of self-luminous heated particles in plasma is based on the use of specialized high-speed video cameras with parallel signal reading. The technical possibilities of using high-speed video cameras for registration of particles in the technological process of plasma spraying of coatings are shown. The use of an optical shutter with a nanosecond resolution makes it possible to measure the particle velocity in the range from 10 to 350 m/s with an accuracy that ensures the calculation of the dynamic parameters of particle acceleration in the jet. The use of a microchannel photomultiplier makes it possible to measure the brightness temperature of particles even at high speeds. The set of experimental data makes it possible to determine the form of the fundamental diagram of a two-phase plasma jet by the value of the particle transfer velocity in the idle mode and the maximum load capacity of the flow. The considered experimental technique makes it possible to measure the dynamic constants of motion and heating of both individual particles in a plasma flow and the fundamental diagram of interaction during collective motion. The proposed diagnostic method is recommended to be used to study the load capacity of two-phase flows, as well as an indicator of the limiting technological state of the plasma torch and the transition to unstable spraying modes.
Oksana Isaeva, Marina Boronenko, Pavel Gulyaev
Open Access
Article
Conference Proceedings
Implementation of an IoT-Based Environment to Control an Industrial Process by Voice Commands using a Virtual Assistant
In recent years the use of virtual assistants has been extended in a large number of applications to provide comfort to the user. This article proposes the development of an IoT (Internet of Things) environment to control an industrial process through voice commands using these devices, where the operator can interact and control the process using his voice. In the first part, a review of works where virtual assistants are used for automation and control processes is made, then the proposed architecture is presented, where we detail the protocols and media used. Next, the development of the system and the validations carried out in an industrial environment are presented, considering its own characteristics. Finally, we detail the conclusions of the project focused on minimizing access times to a control interface, and the growing use of these technologies at different levels of the automation pyramid considering its benefits and limitations
John Guachun- Arias, Luis Serpa-Andrade
Open Access
Article
Conference Proceedings
Assembly Line Optimization Applying a Construction Algorithm
The production of turbochargers is increasing in the Latin American market. However, it is performed in an empirical way. Resource optimization enables an improvement in performance that translates into time and cost reduction. The content of this paper proposes the analysis performed to a company that dedicates to the construction of these equipment, and the development of an improvement proposal based on the Systematic Layout Planning (SLP) method. On-site visits were made to gain direct insights and based on the observations the layout of the plant was developed using LucidChart software. Further, the assembly and operations diagram were created as well as the determination of the process stages. Finally, the process was optimized by applying a constructive algorithm using Computerized Relationship Layout Planning (CORELAP), which evaluated the activities for their proximity and importance. Based on this design, an optimized layout of the company operations and routes was elaborated considering the real conditions of the company. The travel distance was reduced by 71.07%, and the time spent by 84.58%. While analyzing the time spent assembling a turbocharger, a decrease of 49.4% in its values was obtained from the analysis. The results attained from this proposal validate the application of the algorithms. Thus, enabling the elaboration of inferences regarding future long-term economic savings.
Jennifer Mayorga, Jorge Buele, Angel Soria, Manuel Ayala-Chauvin
Open Access
Article
Conference Proceedings
Principal Component Analysis of Inhibiting Factors to the Espousal of Lean Construction in Developing Economies
The inefficiencies plaguing construction processes have negatively impacted the delivery of construction projects. The South African construction industry is not exempted from this as it is still characterized with overwhelming ineffectiveness in construction project actualization. Lean construction offers a variety of innovative concepts that aids the optimization of construction activities. Despite the benefits of the implementation of lean construction, its adoption is clearly not evident in developing economies. This study empirically assesses the inhibiting factors to the adoption of lean construction in the South African construction industry. Data was collected from construction professionals and was analysed with Exploratory Factor Analysis which revealed four constructs as the barriers to the implementation of lean construction. Conclusively, the study recommended that lean construction should be inculcated in the curricular of higher institutions of learning offering built environment related courses; also construction professional bodies should encourage the mandatory training of professionals as an area of competence in judging registration of professionals. The findings from this study brings to the fore the hurdles faced in the construction industry in the adoption of lean construction, hence giving a clear direction on how best to abate these challenges for the attainment of the benefits of its espousal.
Matthew Ikuabe, Clinton Aigbavboa, Douglas Aghimien, Pretty Ramaru, Ayodeji Oke, Opeoluwa Akinradewo
Open Access
Article
Conference Proceedings
Designing and Implementing Simulation Exercises for State Sanitary and Epidemiological Service
The paper presents business processes related to the work of sanitary services in cases of an epidemic of foodborne diseases. On their basis, simulation exercises according to given scenarios were developed. The work is related to the implementation of a project financed by the National Center for Research and Development. The activities of the staff of the county-level State Sanitary Inspectorate were analyzed in terms of actions taken in crisis situations related to the emergence of a large food poisoning outbreak or an epidemic of food-borne infectious disease. The same analysis was carried out in the scope of actions performed by individual teams participating in the simulation exercises. The result of the analysis was presented in the form of business process diagrams made in BPMN notation. The architecture of the simulation exercise support system assumes the use of a number of components responsible for the preparation of data and exercise scenarios, the implementation of exercises in training teams, supervision by exercise management, monitoring of the current course of the exercise, and review after activities.Business processes perfectly illustrate what activities are performed by individual groups of people during exercises and allow for monitoring and measuring indicators of the team’s work effectiveness. Business processes have been divided into two groups of processes. The first group of processes concerns activities performed only by persons exercising. These are processes that describe the activities performed during an epidemiological inquiry. In this case, describing the activities in the form of a process allows the practitioners to increase the speed of reaction in making decisions that directly affect the course of the investigation because they have at their disposal the entire range of data processed by the process along with the full picture of the situation.The second group of business processes describes the activities of the teams for preparing exercises, play-offs, and evaluating the results in the form of a simulation exercise scenario. The activities listed in this group of processes allow the participants of the above-mentioned teams for the efficient management of the tasks of the training team, for monitoring their activities, and for full control of the simulation. The training preparation team receives tasks related to the preparation of the environment and data for a given exercise scenario and the commissioning of individual system components at the start of the simulation exercises. The play-off team receives tasks related to the preparation of answers to the questions of the practitioners, reactions to decisions made by the practitioner team, and the control of the simulation time. The results analysis team receives tasks related to the analysis of the history of processes, the analysis of decisions and actions, the assessment of the course of exercises, and the skills of the training team. Each team receives a full range of data processed by individual processes in this group.The processes of both groups are interconnected. Activities undertaken by the training team within the processes of the first group directly affect the appearance of activities in the processes of the second group. Mutual communication within the performed tasks allows for simulation exercises in accordance with the modeled exercise scenario. The simulation exercise support system records each action and decision of the participants in the history of the processes along with the exact timestamp and a record of who performed the action. The concept of the AAR subsystem (after action review) is based on historical data of tasks performed within the framework of the processes, enabling the reconstruction of the course of the exercise with the possibility of starting the exercise from a selected moment. The paper will also present the methodology of designing interfaces for a system of computer-aided simulation exercises.
Robert Waszkowski, Tadeusz Nowicki, Agata Chodowska Wasilewska
Open Access
Article
Conference Proceedings
Low-code Development Platform for Business Process Automation: Aurea BPM
The paper introduces overall low-code platform architecture for business process automation. The architecture assumes the division of the platform into subsystems organized in the substantive layer, as well as in the layers of system management and integration. The substantive layer consists of the Design and Development, Metadata Repository, Deployment, and Runtime subsystems. The most important of them are Design, Development, and Runtime. The former allows for the development of process models in the form of diagrams and metadata, while the latter is responsible for running applications in the target environment and delivering them to end-users. Models developed in the Design and Development subsystem are stored in the Metadata Repository subsystem, which is additionally responsible for providing users with controlled user access to system resources.Designed and approved process models are made executable in the Deployment subsystem. The models prepared in this way are used by the Runtime subsystem, delivering a ready-to-use application to end-users.The article presents the architecture of the solution and the individual steps of implementing an exemplary business process.
Robert Waszkowski
Open Access
Article
Conference Proceedings
Process Safety in electrolytic green hydrogen production
The article objective is to analyze the electrolytic process of green hydrogen production from process safety and process safety management (PSM) points of views. The green hydrogen through water electrolysis production of is emerging as one of the main and best alternatives to replace the use of fossil fuels and thus mitigate environmental pollution and its consequences to the planet. For this purpose, the principles of the electrolysis process were established, as well as the different ways to carry it out, among which are: Alkaline electrolysis (AE); Proton exchange membrane (PEM) electrolysis and High-Temperature electrolysis (HTE). Its associated hazards and risks were mentioned, and the Dow Fire and Explosion Index (F&EI) was calculated for the three electrolysis methods, obtaining similar results with each other. In addition, the Canadian Society for Chemical Engineering (CSChE) PSM standard and the main international standards must be applied to electrolytic hydrogen production systems, such as: ISO 31000:2018 ; ISO 15916:2015 and ISO 22734:2019, was observed. Like other fuels, hydrogen processes production must be managed with preventive measures avoid events may have negative consequences to people, structures, and surrounding environment.
Rodrigo Dominguez, Enrique Calderón, Jorge Bustos
Open Access
Article
Conference Proceedings